Briquetting Industry, Technlogy and Progress
صنعت بریکت سازی، انتخاب تکنولوژی و مسیر توسعه
امروزه بریکت سازی به عنوان صنعتی شناخته شده در زمینه فرآوری مواد جانبی ایجاد شده در صنایع مختلف مطرح می باشد. با استفاده از این تکنولوژی، مواد با دانه بندی ریز و ناهمگن به بریکت هایی با ابعاد و شکل مشخص تبدیل شده، به طوری که بهبود عملکرد آنها در کاربرد مورد نظر را در پی خواهد داشت.
تکنولوژی بریکت سازی از قدمتی حدود 200 ساله برخوردار بوده به طوری که صنایع مختلفی از آن، جهت بهبود عملکرد فرآیند های خود استفاده می کنند.
فلسفه وجودی صنعت بریکت سازی را می توان “استفاده بهینه از مواد جانبی و کم بازده تولید شده در صنایع مختلف” عنوان کرد. اما در دهه اخیر کاربردهای جدیدی از صنعت بریکت سازی معرفی شده که اهمیت این صنعت را بیش از پیش نمایان کرده است.
استفاده بهینه از مواد جانبی تولید شده در هر صنعتی، همواره به عنوان چالشی بزرگ جهت نیل به شعار توسعه پایدار و افزایش بهره وری تولید در آن صنعت مطرح بوده است. در اکثر صنایع، در حین فرآیند تولید، همواره مقادیری مواد جانبی ایجاد می گردد که عمدتا به واسطه دانه بندی ریز، امکان استفاده مؤثر از آنها وجود ندارد. لذا این مواد که گاها ارزش قابل توجهی نیز دارند تنها به واسطه محدودیت های ابعادی، نمی توانند مانند مواد درشت دانه تر مورد استفاده قرار گیرند. این موضوع می تواند اثرات منفی قابل توجهی بر راندمان تولید و همچنین توجیه پذیری اقتصادی فعالیت صنایع مورد نظر داشته باشد. در اینجاست که نقش تکنولوژی بریکت سازی نمایان شده به طوری که با کمک آن می توان استفاده مؤثر از مواد جانبی را میسر نمود. بدین ترتیب هم مواد جانبی ارزشی معادل و گاهی بیشتر از مواد اصلی پیدا می کنند و هم از بروز مشکلات زیست محیطی پیرامون ورود این مواد به طبیعت جلوگیری خواهد شد.
زمینه های کاربردی صنعت بریکت سازی:
از جمله صنایعی که به طور گسترده از این تکنولوژی استفاده می نمایند می توان به موارد زیر اشاره نمود:
- آهن و فولاد (آهن اسفنجی، مواد جانبی واحد های احیای مستقیم و فولادسازی)
- مواد معدنی (زغال سنگ، کک، دولومیت، منگنز، فروآلیاژ ها، آلومینا، آهک و … )
- مواد شیمیایی (سولفات ها، کربنات ها، کلرید ها، سیانید ها، برومید ها و …)
- کودهای شیمیایی کشاورزی
- مواد شوینده و بهداشتی
یکی از قدیمی ترین زمینه های کاربرد تکنولوژی بریکت سازی، صنعت زغال سنگ است. در طی تمدن بشری، زغال سنگ همواره به عنوان یکی از منابع اصلی انرژی شناخته شده است. از طرف دیگر، این ماده به عنوان عامل احیاء کننده (Reductant) در بسیاری از صنایع تولید فلزات مورد استفاده قرار می گیرد. اما در حین فرآیند استخراج زغال سنگ، همواره مقادیر قابل توجی نرمه زغال سنگ بدست می آید (5 تا 10 درصد) که همان طور که پیش تر اشاره گردید، به واسطه محدودیت های ابعادی، جهت استفاده مؤثر از آن از تکنولوژی بریکت سازی استفاده می شود. بریکت تولید شده از نرمه زغال سنگ به واسطه دانه بندی و شکل ظاهری یکنواخت و همچنین دانسیته بیشتر در مقایسه با زغال سنگ، معمولا از ارزش اقتصادی و عملکرد مطلوب تری برخوردار است.
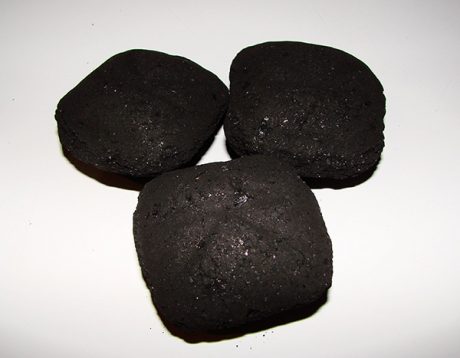
از دیگر زمینه های کاربردی صنعت بریکت سازی می توان به صنعت احیای مستقیم اشاره نمود. گندله سنگ آهن با عبور از کوره احیای مستقیم و قرار گیری در محیط احیائی، اکسیژن خود را از دست داده و به آهن اسفنجی (با دانه بندی 6 تا 16 میلیمتر) تبدیل می گردد. محصول خارج شده از کوره احیای مستقیم معمولا دارای 5 تا 10 درصد نرمه آهن اسفنجی (با دانه بندی کوچک تر از 6 میلیمتر) است که در صورت استفاده از گندله بی کیفیت، میزان تولید نرمه افزایش خواهد یافت. حال در صورتی که نرمه آهن اسفنجی به کوره فولادسازی شارژ شود، به واسطه اندازه ریز آن، توسط جریان هوای خروجی از کوره، از محیط کوره خارج شده و عملا تلفات آهن را به طور قابل توجهی افزایش می دهد. در حدود نیم قرن است که از تکنولوژی بریکت سازی به عنوان راه حل این مشکل استفاده می شود. بدین صورت که محصول خروجی از کوره احیای مستقیم با عبور از سیستم اسکرین، غربال شده و نرمه ریز دانه از محصول اصلی جدا می گردد. حال نرمه آهن اسفنجی توسط سیستم بریکت سازی به بریکت نرمه آهن اسفنجی تبدیل شده و قابلیت شارژ به کوره فولادسازی را پیدا می کند. بدین ترتیب با بهره گیری از تکنولوژی بریکت سازی راندمان مصرف آهن اسفنجی به طور قابل توجهی بهبود پیدا خواهد نمود. از طرف دیگر، از دهه 80 میلادی انقلابی در صنعت آهن و فولاد رخ داد به طوری که با ادغام دو تکنولوژی احیای مستقیم و بریکت سازی در دمای بالا، محصولی با نام بریکت داغ آهن اسفنجی (HBI) پدید آمد که بسیاری از مشکلات پیرامون ذخیره سازی و حمل و نقل آهن اسفنجی و همچنین شارژ این محصول به کوره های فولادسازی را مرتفع کرده به طوری که امروزه سیستم های بریکت سازی به جزئی جدایی ناپذیر از صنعت احیای مستقیم مبدل شده اند.
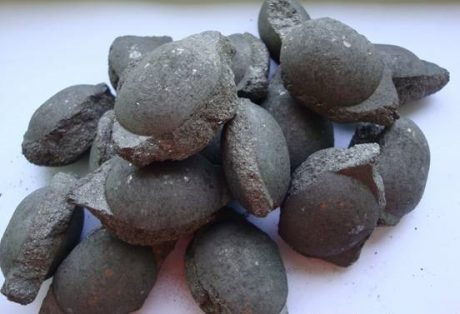
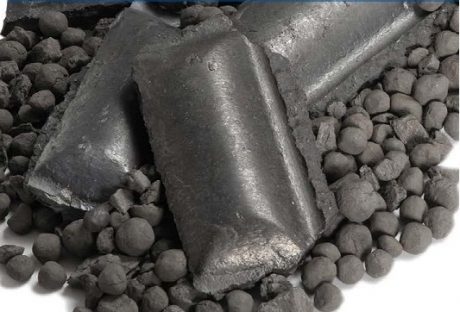
علاوه بر این در طی چند سال اخیر زمینه جدیدی در حوزه کاربرد تکنولوژی بریکت سازی در صنعت احیای مستقیم ایجاد شده است که هدف از آفرینش آن تولید محصولی با کیفیت و در عین حال، دارای خواص مورد نیاز واحد های فولادسازی می باشد. این محصول که با نام بریکت سرد آهن و کربن (CBIC) شناخته می شود، در طی فرآیند بریکت سازی آهن اسفنجی در دماهای پایین تولید می گردد. از مزایای این محصول نسبت به آهن اسفنجی، می توان به استحکام خردایش و مقاومت به سایش بیشتر، مقاومت به افت درجه فلزی بیشتر، دانسیته بالاتر و همچنین ریسک بسیار کمتر در ذخیره سازی و حمل و نقل اشاره نمود. از طرف دیگر، در فرآیند تولید این محصول، امکان افزودن افزودنی های مورد نیاز واحد فولادسازی مثل کربن، آهک و فروآلیاژها و در نتیجه، تنظیم ترکیب شیمیایی شارژ ورودی به کوره فولادسازی نیز وجود دارد. تمام این مزایا موجب خلق ارزش افزوده قابل توجه نسبت به آهن اسفنجی می شود که صنعت احیای مستقیم را برای همیشه مدیون تکنولوژی بریکت سازی کرده است.
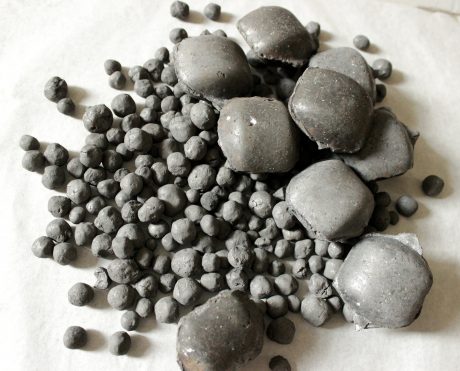